What are material modes of failure?
In our previous article we looked at the properties of engineering materials. In this article, we’re going to dive into material modes of failure and what they are.
What is failure?
The definition of failure is that the component is no longer fit for use or its designed purpose. This can be caused by several different mechanisms, and is a breakdown of the material in some way. We’re going to look at some of the common types of material failures.
Ductile Failure
The image below shows the typical shape of the stress-strain graph for a ductile material:
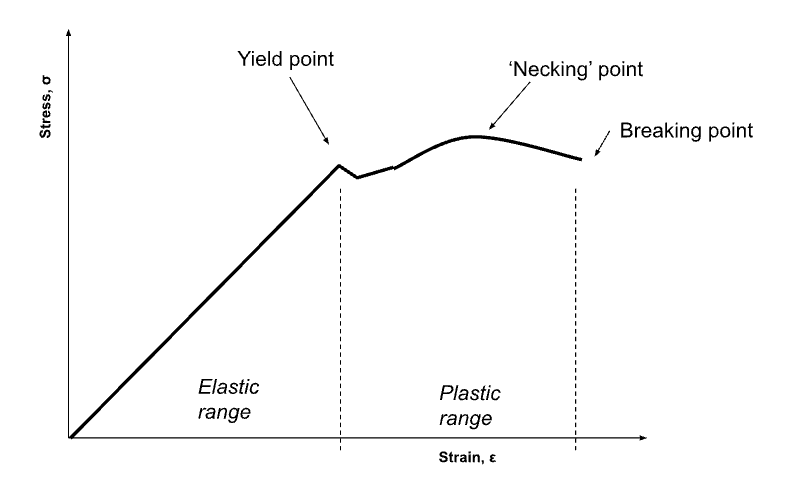
Failure in a ductile material occurs in two stages:
- Once the material has passed its yield point and plastic deformation has occurred.
- At the ultimate breaking point of the material when the rupture occurs.
The images below show the sequence of failure of a ductile material. Notice how the material moves from extension (elastic deformation), into plastic deformation, then fails when the material breaks apart.
This typically results in a ‘cup and cone’ failure, named due to the shape of the material at the rupture point.
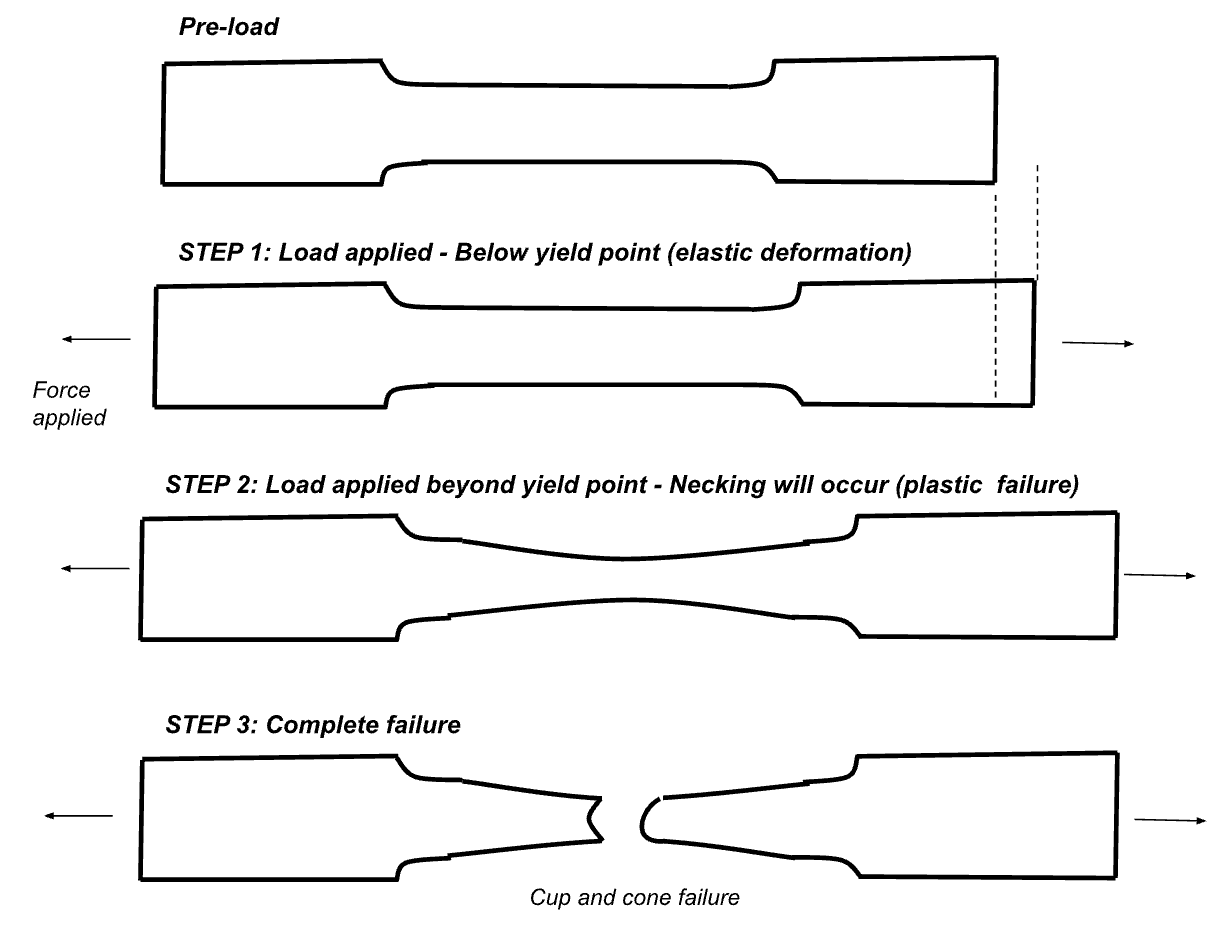
Brittle Fracture
With a brittle fracture, the material doesn’t go through the plastic deformation phase. Instead, it breaks with a sudden crack. Brittle materials can still be strong, but once load passes its UTS, the material can fail quickly with little or no further resistance. An example of this is cast iron, which is strong but brittle.
The typical stress-strain curve for a brittle material is shown below:
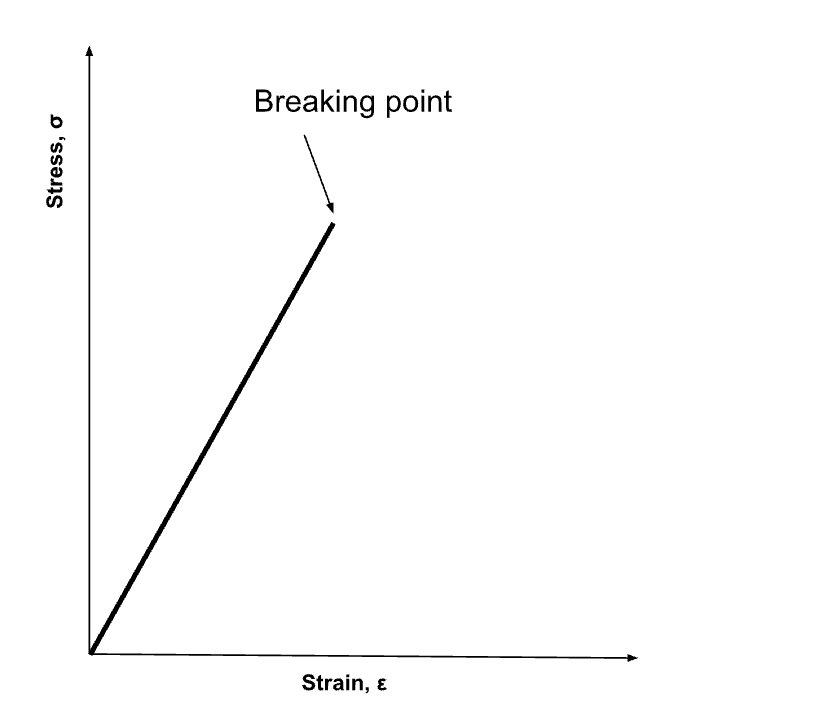
The image below shows the failure modes. As you can see there is no warning that the material will soon fail. From an engineering perspective this means we need to be careful as these materials will fail suddenly and catastrophically.
A good example of this is engineering composite materials, such as CRFP. The material can still bend, but at a given load the material will fail without warning.
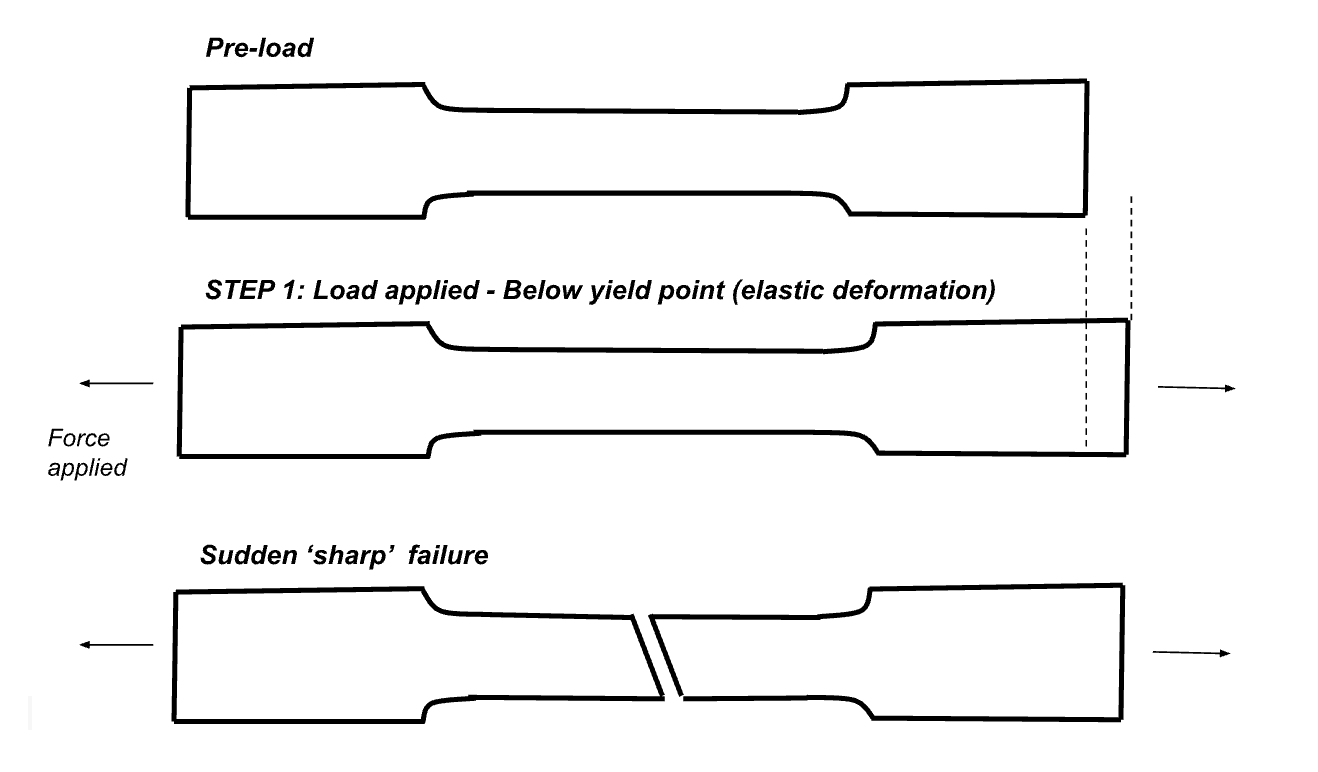
Brittle materials are also prone to cracking caused by an imperfection in the material. This can be a notch or a sharp corner in a component design. These features raise the local stress level, known as stress concentration areas.
Fatigue
Fatigue is an important concept to understand in engineering. It’s the failure of a component under cyclic (repeated) stress. This can happen even if this stress is below the material’s yield stress.
Think of a metal paperclip. If we straighten the paperclip, it can bend without a problem. Now imagine we repeatedly bend the paperclip by the same amount over and over, eventually it will stiffen and then break. This is what fatigue looks like.
The fatigue strength of a component can be defined as the level of stress needed to cause failure after a certain number of cycles. This is often represented on a S-N graph, where the S stands for Strength and N stands for number of cycles. An example of a S-N chart is shown below:
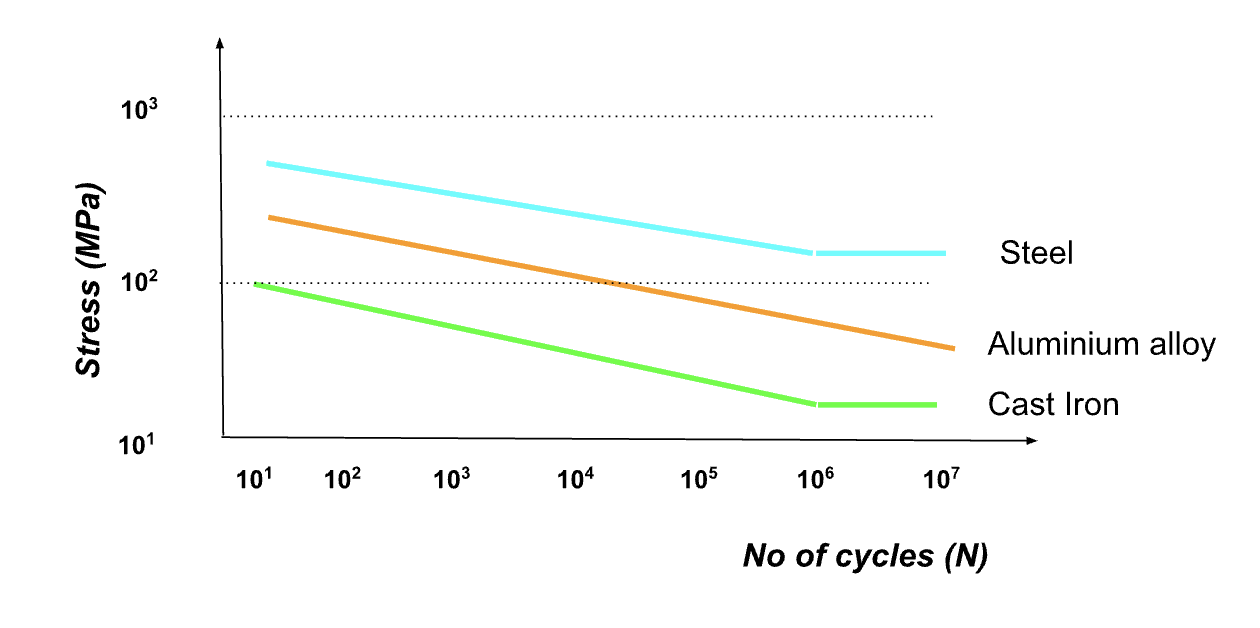
For some materials, the line straightens out. This lower limit for the material is known as the endurance limit, given the symbol, σE. The endurance limit is found in ferrous materials, and a good approximation for an engineer to use is 0.3 x the tensile strength of the material.
Notice how Aluminium (and all non-ferrous metals) do not have a clear endurance limit. Instead we should quote the stress level to cause failure for a given number of cycles, given the symbol σN, where N is the number of cycle., e.g. σ10E3 would be the stress level that will cause the material to fail at 10,000 cycles.
Creep
Creep is a mechanism where a material stretches over time when exerted to a constant tensile stress. The material can subsequently fail even if the applied stress is below the ultimate tensile strength of the material. Most material doesn’t exhibit creep until a certain level of stress is applied. This minimum level is known as the limiting creep stress.
Temperature has a significant effect on a material’s vulnerability to creep. Generally, if we increase a material’s temperature, its limiting creep stress will reduce. This means creep will start to occur at a lower level of stress.
One important application for designing against creep is that in gas turbine engines. The turbine blade operates for a significant time at a high temperature, therefore the turbine blades will have a tendency to increase in length under the high centrifugal force applied by the rotation of the engine. Obviously if it was to increase to such an extent that it touches the inside of the engine cowling, this would be catastrophic. Careful consideration of material choice, and creep characteristics must be taken into account.
Degradation
Other failure modes of materials are concerned with some sort of erosion or degradation:
- Corrosion – the chemical changes of a material caused by the presence of another element. For example, oxygen on some metals can cause them to produce an oxide layer that can change the mechanical properties of that material.
- Galvanic corrosion – this type of corrosion can happen between two solid materials. It’s an electrochemical change caused by two dissimilar materials coming into contact. It is caused by a potential difference of the two materials, and when exposed to an electrolyte causes an electrochemical reaction to occur.
Keep an eye out for our next articles looking at elastic and magnetic hysteresis.
Interested in our courses?
You can read more about our selection of accredited online mechanical and industrial engineering courses here.
Check out individual courses pages below:
Higher International Diploma in Mechanical Engineering
Higher International Certificate in Mechanical Engineering
Diploma in Mechanical Engineering
Diploma in Mechanical Technology
Higher International Diploma in Industrial Engineering
Higher International Certificate in Industrial Engineering
Diploma in Engineering Management
Alternatively, you can view all our online engineering courses here.
Recent Posts
Essential Formulas for Calculating Drilling Parameters
Essential Formulas for Calculating Drilling Parameters When it comes to precision and efficiency in manufacturing, few processes are as foundational—or as critical—as drilling. Whether you’re a seasoned engineer or a student entering the world of mechanical or industrial engineering, understanding how to correctly calculate drilling parameters can significantly impact the quality of your work, the […]
From Raw Material to Refined Component: The Role of Drilling and Turning
From Raw Material to Refined Component: The Role of Drilling and Turning Secondary processes are used in manufacturing to further modify the output of primary manufacturing processes in order to improve the material properties, surface quality, surface integrity, appearance and dimensional tolerance. In this blog, we will focus on drilling and turning as secondary manufacturing […]
Behind the Cutter: How Milling Shapes the Future of Manufacturing
Behind the Cutter: How Milling Shapes the Future of Manufacturing Secondary processes are used in manufacturing to further modify the output of primary manufacturing processes in order to improve the material properties, surface quality, surface integrity, appearance and dimensional tolerance. In this blog, we will focus on milling as a secondary manufacturing process. Machining refers […]